Funktionsweise und Anwendungsfälle
Digitaler Zwilling
Ein digitaler Zwilling ist eine virtuelle Repräsentation eines physischen Objekts oder Systems. Wir erklären, wie digitale Zwillinge funktionieren und wofür sie in der Industrie eingesetzt werden.
1. Was ist ein digitaler Zwilling?
Ein digitaler Zwilling (engl.: „Digital Twin“) ist eine virtuelle Repräsentation eines physischen Objekts oder Systems. Der digitale Zwilling basiert auf Daten und Modellen über sein Gegenstück in der realen Welt und bildet dessen Eigenschaften, Zustände und Verhaltensweisen ab.
In der Industrie können digitale Zwillinge z.B. einzelne Produkte oder Maschinen, aber auch ganze Produktionsstandorte repräsentieren.
Ein digitaler Zwilling kann mit dem realen Objekt über einen kontinuierlichen Datenaustausch verbunden sein, kann aber auch als geschlossenes System mit eigener Datenverarbeitung konzipiert werden.
Indem ein digitaler Zwilling kontinuierlich mit Daten über das reale Objekt oder System versorgt wird, lässt sich bei Bedarf ein nahezu identisches und synchronisiertes Echtzeit-Abbild schaffen, das sowohl rückwirkende und aktuelle Analysen als auch Tests, Simulationen und Zukunftsprognosen möglich macht.
Die Daten, auf denen ein digitaler Zwilling basiert, können aus verschiedensten Quellen stammen. Neben Sensoren und IoT-Geräten, können z.B. Informationen aus Quellen wie MES, ERP-Systemen oder historischen Datenbanken herangezogen werden.
Oft führt ein digitaler Zwilling eine Vielzahl an Daten in einem digitalen Abbild zusammen. Diese können von Projekt- und Auftragsdaten über Fehlerdokumentationen und Qualitätskontrolldaten bis hin zu Umgebungsparametern und Daten aus dem Produktionsprozess reichen. Auch Branchendaten, projektbezogene Zielvorgaben oder Nutzungsdaten des physischen Objekts können eine wichtige Rolle spielen.
Digitale Zwillinge können viele verschiedene Formen annehmen, abhängig vom Anwendungsfall, und unterscheiden sich zum Teil auch stark in ihrer Komplexität. In der Praxis können sie sowohl zu Test-, Simulations- und Schulungszwecken als auch zur Überwachung und Steuerung des realen Gegenstücks eingesetzt werden.
2. Wofür werden digitale Zwillinge in der Industrie eingesetzt?
Im Folgenden listen wir häufige Einsatzgebiete für digitale Zwillinge in der Industrie auf. Die exakte Umsetzung des Zwillings ist dabei stets abhängig vom geplanten Einsatzzweck und den Eigenschaften des nachzubildenden Objekts oder Systems. Da sich diese Faktoren von Fall zu Fall unterscheiden, sind die spezifischen Anforderungen und Implementierungsdetails für jedes Projekt individuell.
Anlagenüberwachung und Problemdiagnose:
Digitale Zwillinge können eine Benutzerschnittstelle zur effektiven Überwachung von Produktionsanlagen bereitstellen. Durch die Konsolidierung aller Daten und Kennzahlen zu einer Maschine in einem digitalen Zwilling, können Unternehmen den Anlagenzustand am digitalen Abbild in Echtzeit überwachen und mögliche Anomalien, Probleme oder Trends erkennen.
Oft erfolgt eine Visualisierung wichtiger Daten über eine benutzerfreundliche Oberfläche.
Digitale Zwillinge zur Anlagenüberwachung integrieren z.B. Sensordaten wie Temperatur, Druck oder Vibrationen sowie (historische) Leistungs- und Betriebsdaten.
Wird ein digitaler Zwilling erstellt, der das Verhalten der realen Anlage nachbildet, können Probleme und Optimierungsmöglichkeiten auch dadurch erkannt werden, dass das Verhalten des digitalen Zwillings von dem Verhalten des realen Objekts abweicht.
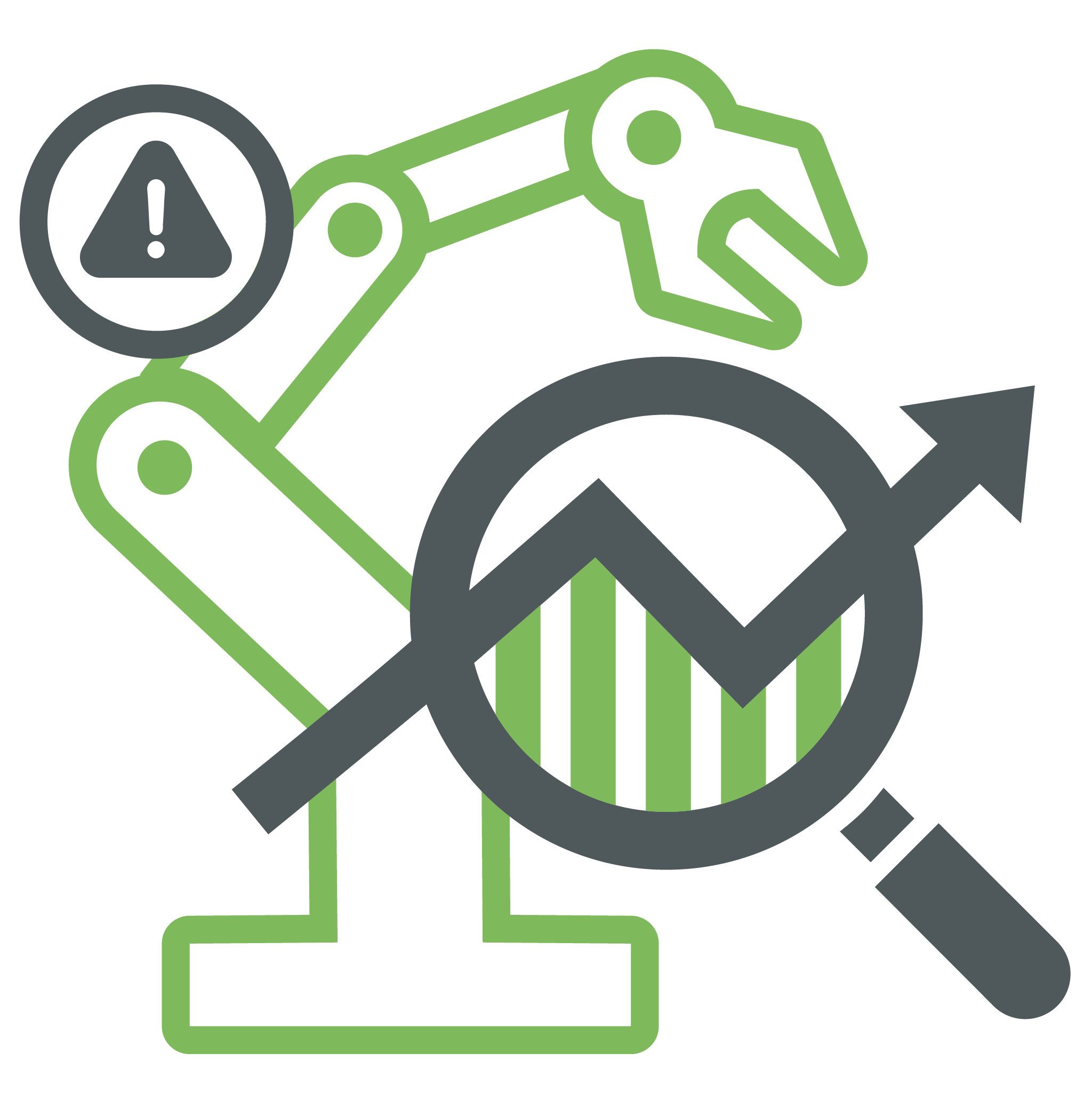
Instandhaltung:
Digitale Zwillinge von Produktionsanlagen und Maschinen ermöglichen sowohl präventive als auch die prädiktive Instandhaltungsstrategien.
Durch die Erfassung und Kombination von Daten aus verschiedenen Quellen und die Synchronisation des digitalen Abbilds mit dem physischen System, können Unternehmen Analysen durchführen, um den optimalen Wartungszeitpunkt zu ermitteln.
Insbesondere können verschiedene Daten zueinander in Verbindung gesetzt werden, um komplexe Zusammenhänge zu identifizieren. Auch hier können Unterschiede zwischen dem digitalen Zwilling und dem Referenzobjekt z.B. auf Verschleiß einer Maschine hindeuten.
Virtuelle Inbetriebnahme:
Digitale Zwillinge bieten eine Möglichkeit, neue Anlagen noch vor ihrer physischen Inbetriebnahme in einer virtuellen Umgebung zu testen und zu optimieren, um späteren Kosten- und Zeitaufwand für Nacharbeiten, Fehlerbehebungen und Ausfälle zu vermeiden.
Dazu wird zunächst ein detailliertes, digitales Modell der Anlage erstellt (z.B. mithilfe von CAD-Daten). Dieses wird in einer digitalen Umgebung betrieben und dabei beispielsweise an die vorgesehene Steuerungstechnik angebunden, um das Systemverhalten unter verschiedenen Bedingungen und Szenarien zu testen.
Produktoptimierung:
Digitale Zwillinge können eingesetzt werden, um das Design, die Qualität oder die Leistung von Produkten zu optimieren – oft noch vor ihrer Markteinführung.
Auch hier wird eine möglichst detaillierte digitale Nachbildung des Produkts und seiner physikalischen Eigenschaften erstellt. Als Basis dienen z.B. 3D-Modelle, Designinformationen, Prototypen, gesammelte Nutzungsdaten oder Daten aus dem Herstellungsprozess.
Anschließend können Simulationen mithilfe spezieller Software durchgeführt werden, um Optimierungspotenziale, Schwachstellen oder Belastungsgrenzen zu identifizieren.
Bei den Produkten könnte es sich z.B. um Fahrzeugkomponenten wie Motoren oder elektronische Geräte aus dem Haushalt handeln.
Simulationen und Tests:
Ein besonderes Merkmal digitaler Zwillinge ist die Möglichkeit, Änderungen an bestehenden Strukturen und Prozessen im Vorfeld ausführlich zu testen, ohne dazu in den laufenden Betrieb eingreifen zu müssen.
Mithilfe verschiedenster Simulationen und Tests können die Auswirkungen von Optimierungsmaßnahmen geprüft und notwendige Anpassungen noch vor der Implementierung vorgenommen werden.
Die Einsatzszenarien sind vielfältig und reichen von Änderungen an Produktionsvorgaben oder Prozessparametern bis hin zu komplexen Anpassungen der Systemarchitektur oder der Integration neuer Technologien.
Training und Weiterbildung:
Digitale Zwillinge werden in der Industrie zunehmend auch zu Schulungszwecken eingesetzt. Je nach Umsetzung, kann eine sichere und kontrollierte Umgebung geschaffen werden, in der Mitarbeitende wiederholt verschiedene Szenarien und Arbeitsvorgänge durchlaufen können. Dabei wird weder der Betrieb gestört, noch riskieren Unternehmen Schäden an realen Anlagen.
Gleichzeitig lassen sich praxisnahe Trainingsprogramme gestalten, die Mitarbeitende auf reale Szenarien vorbereiten. Diese könnten z.B. die Wartung und Bedienung von Anlagen, aber auch das Verhalten in Notfallsituationen umfassen.
3. Wie wird ein digitaler Zwilling erstellt?
In diesem Abschnitt erläutern wir typische Phasen, die in der Entwicklung und Einführung eines digitalen Zwillings durchlaufen werden. Dabei ist jedoch zu beachten, dass die exakten Arbeitsschritte zur Erstellung eines digitalen Zwillings in der Praxis stark variieren. Dies ist vor allem dadurch bedingt, dass jedes abzubildende Objekt oder System seine individuellen Merkmale aufweist. Auch die Umsetzung des digitalen Zwillings selbst (Datenbasis, Visualisierung, Benutzerschnittstellen) ist immer von den individuellen Anforderungen abhängig.
In manchen Fällen wird ein digitaler Zwilling erstellt, bevor das Referenzobjekt existiert. Dies kann z.B. bei der Konzeption und Entwicklung neuer Produkte der Fall sein.
3.1. Ziele und Anforderungen definieren
In der Regel wird ein digitaler Zwilling mit einer bestimmten Zielsetzung eingeführt. Daraus ergeben sich verschiedene Anforderungen:
- Welche Teilbereiche des physischen Objekts oder Systems müssen nachgebildet werden?
- Muss der digitale Zwilling das Referenzsystem in Echtzeit abbilden?
- Welche Daten werden benötigt und aus welchen Quellen stammen diese?
- Wie erfolgt die Integration mit bestehenden IT-Systemen und -Prozessen?
- Welche Benutzerschnittstellen werden benötigt, um den digitalen Zwilling optimal einzusetzen?
- Welche Sicherheitsmaßnahmen müssen getroffen werden?
- Welche Schulungsmaßnahmen sind notwendig, um den digitalen Zwilling effektiv zu nutzen?
Die genaue Definition und Dokumentation der Anforderungen an einen digitalen Zwilling ist die Grundlage für dessen reibungslose Entwicklung und Inbetriebnahme. Da es sich bei vielen digitalen Zwillingen um äußerst komplexe Systeme handelt, müssen Unternehmen bereits früh sicherstellen, dass die notwendigen (Mitarbeiter-)Kompetenzen zur Verfügung stehen. Dies betrifft sowohl die Erstellung eines digitalen Zwillings als auch dessen Nutzung im Arbeitsalltag.
3.2. Datensammlung und -integration
Grundvoraussetzung für die Erstellung und den Betrieb eines Digitalen Zwillings ist die Sammlung, Aufbereitung und Zusammenführung relevanter Daten.
Ein wichtiger Schritt ist daher die Bestimmung der erforderlichen Datenquellen und benötigten Daten. Einige mögliche Datenquellen sind im Folgenden aufgelistet:
- Sensoren (z.B. Temperatursensoren, Vibrationssensoren, Positionssensoren)
- historische Datenbanken (z.B. Datenbanken für historische Betriebs- und Wartungsdaten)
- CAD-Modelle (geometrische und strukturelle Informationen)
- MES und ERP-Systeme (Informationen über Produktions- und Geschäftsprozesse)
- Externe Datenquellen (z.B. APIs für Markt- und Branchendaten)
Der nächste Schritt ist die Einrichtung fehlender Datenquellen (z.B. Installation und Konfiguration neuer Sensoren) sowie die Anbindung der bereits vorhandenen Datenquellen.
Dabei muss sichergestellt werden, dass Systeme über sichere Schnittstellen angesprochen und Daten über geeignete Protokolle bereitgestellt werden können. Möglicherweise muss auch eine kontinuierliche Datenübertragung in Echtzeit zwischen einer realen Anlage und einem digitalen Zwilling gewährleistet werden. Und nicht zuletzt muss auch die Netzwerkinfrastruktur für eine sichere Datenübertragung geeignet sein.
Da es sich bei vielen Datenquellen um Sensoren und andere internetfähige Geräte handelt, ist der digitale Zwilling eng mit der Umsetzung des Industrial Internet of Things (IIoT) verknüpft.
Daten müssen gegebenenfalls in bestimmte Formate konvertiert, durch Operationen wie Filtern und Normalisieren vorverarbeitet und auf einer zentralen Plattform zusammengeführt werden. Dort muss ein geeignetes Datenmodell vorhanden sein, dass alle benötigten Daten integriert.
Zu den größten Herausforderungen im Bereich der Datenintegration zählen inkompatible Protokolle und Schnittstellen, mögliche Sicherheitslücken oder eine zu geringe Flexibilität, Skalierbarkeit oder Zukunftssicherheit eingesetzter Lösungen.
In der Praxis kommen an vielen Stellen industrielle Standdardschnittstellen und -protokolle wie OPC UA und MQTT zum Einsatz. Insbesondere OPC UA bietet die Möglichkeit, Maschinen- und Gerätedaten herstellerunabhängig in einem einheitlichen Format bereitzustellen.
Integrationswerkzeuge wie OPC Server und IoT Gateways helfen dabei, Kommunikationswege zwischen unterschiedlichen Systemen zu überbrücken und Daten aus der Feldebene sicher an übergeordnete Softwaresysteme oder Cloud-Plattformen zu übermitteln.
Der KEPServerEX bietet Unternehmen eine einheitliche Konnektivitätsplattform für die Erfassung und Bereitstellung industrieller Daten.
Als etablierter OPC UA Server mit integriertem IoT Gateway ermöglicht er die gezielte Einbindung verschiedenster Maschinen und Geräte in eine moderne IT-Infrastruktur – einschließlich älterer Anlagen. Ausgewählte Daten können in standardisierten Formaten für andere Systeme wie MES, ERP oder Cloud-Plattformen bereitgestellt werden. Um Maschinen und Geräte herstellerunabhängig als Datenquellen zu erschließen, implementiert der KEPServerEX mehr als 150 Treiber. Mit der Enterprise-Lösung Kepware+ wird eine unternehmensweite Skalierbarkeit gewährleistet.
Der OPC Server von Kepware
Mit mehr als 150 Treibern erschließt der KEPServerEX Maschinen und Geräte verschiedenster Hersteller als Datenquellen und stellt Industriedaten in Formaten wie OPC UA für andere Systeme bereit.
3.3. Erstellung des digitalen Abbilds
In dieser Phase wird ein möglichst exaktes digitales Abbild des realen Objekts oder Systems erstellt. Dieses muss in der Lage sein, die relevanten Eigenschaften und Verhaltensweisen seines physischen Gegenstücks nachzubilden, um eine zuverlässige Basis für Simulationen, Analysen und Optimierungen zu bieten.
Die Erstellung eines digitalen Modells kann in mehreren Schritten erfolgen:
- Datenmodellierung: Organisation der gesammelten Daten in logische Strukturen, Hinzufügen von Metadaten
- Geometrische Modellierung: Nutzung von CAD-Software zur Erstellung detaillierter 3D-Modelle des physischen Objekts oder Systems
- Physikalische Modellierung: Definition von Materialeigenschaften und Bewegungsabläufen, Einbeziehung von Umgebungsbedingungen
- Verhaltensmodellierung: Definition der Systemzustände, Übergänge und Fehlermodi
- Integration der Steuerung: Integration der realen Steuerungssysteme in das digitale Modell
- Validierung und Verifikation: Durchführung von Testläufen und Simulationen, Abgleich von Ergebnissen mit realen Daten
Je nachdem, welche Funktionen ein digitaler Zwilling erfüllen soll, können weitere Komponenten hinzugefügt werden. Dazu zählen z.B. Methoden zur Echtzeit-Datenanalyse und Algorithmen zur Bestimmung von Wartungsbedarf, aber auch Schnittstellen für die Systemsteuerung und effektive Möglichkeiten zum Durchführen von Simulationen oder Tests.
Besonders wichtig ist auch die Schaffung benutzerfreundlicher Bedienungsoptionen für Endanwender, sodass die vorgesehene Zielgruppe den digitalen Zwilling optimal nutzen kann.
3.4. Einführung, Betrieb und Verbesserung
In der Regel ist die Einführung eines digitalen Zwillings mit Mitarbeiterschulungen verbunden, um Personal optimal auf die Arbeit mit der neuen Technologie vorzubereiten. Gegebenenfalls sind auch Abstimmungen mit Geschäftspartnern und anderen Stakeholdern notwendig.
Nach Einführung des digitalen Zwillings erfolgt eine Evaluierung der Nutzung um Hinblick auf den resultierenden Nutzen und mögliche Optimierungspotenziale.
Vor allem größere Konzerne führen digitale Zwillinge nicht selten als Pilotprojekte an einzelnen Standorten ein. Erweist sich ein solches Projekt als Erfolg, steht als Nächstes oft die Ausweitung auf weitere Standorte an. Gerade in einem solchen Fall ist die frühe und ausführliche Dokumentation aller Projektschritte und Erkenntnisse von hoher Bedeutung.
Weitere Informationen
Was ist OPC UA?
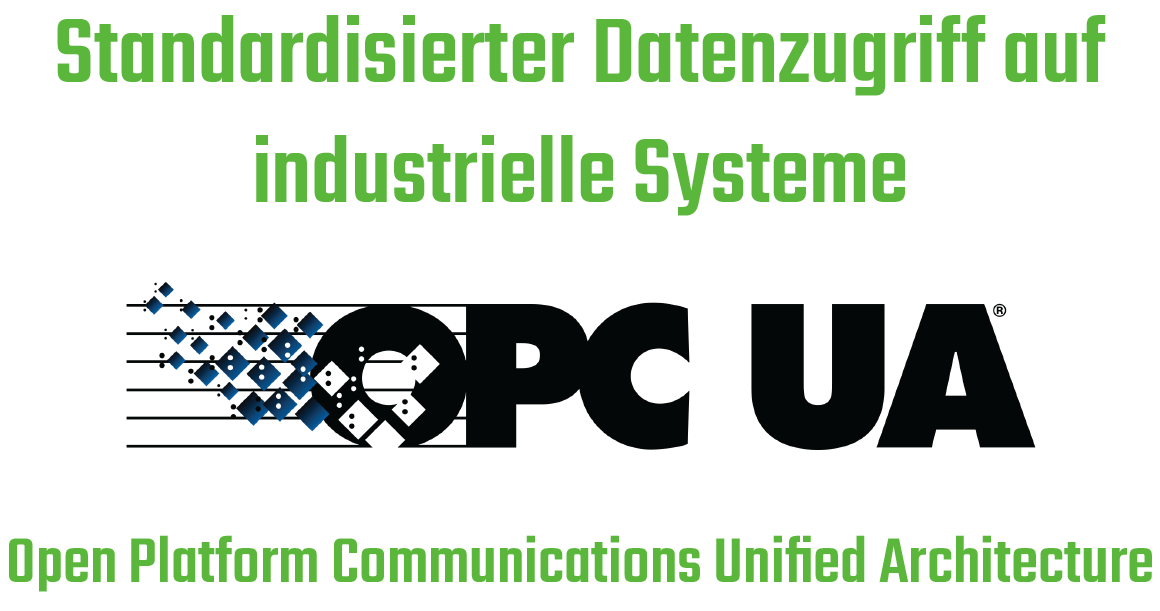
OPC UA ist das führende Standardprotokoll für industrielle Kommunikation. Als solches ermöglicht es den herstellerunabhängigen Datenaustausch zwischen Steuerungen, Geräten, Software und zahlreichen anderen Systemen. Erfahren Sie in unserem Beitrag „Was ist OPC UA“ alles Wichtige über die Funktionsweise des industriellen Kommunikationsstandards, seine Vorteile sowie das umfangreiche Sicherheitskonzept.
Das Kepware IoT Gateway
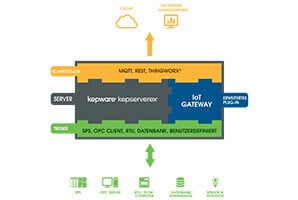
Mit dem Kepware IoT Gateway des KEPServerEX streamen Sie Daten angebundener Maschinen und Geräte direkt in die Cloud. Dabei nutzt das Kepware IoT Gateway die IoT-Standardprotokolle MQTT und REST. In Verbindung mit den zahlreichen Treibern und Suiten des KEPServerEX integrieren Sie auf diese Weise auch ältere Anlagen in eine moderne IIoT-Infrastruktur.
KEPServerEX – Die industrielle Konnektivitätsplattform
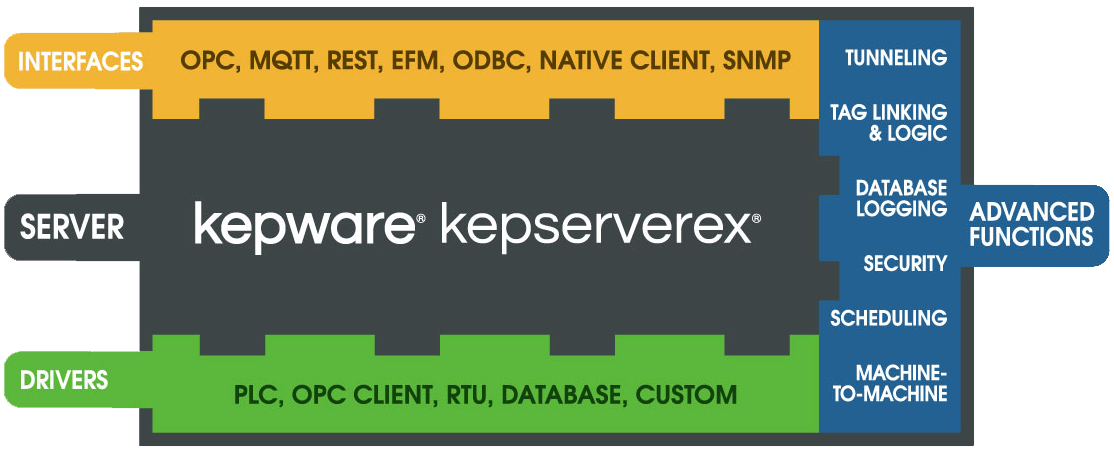
Der KEPServerEX ist die ideale Lösung, wenn es um die Anbindung älterer Anlagen sowie Maschinen unterschiedlicher Hersteller geht. Mit über 160 Treibern und 34 Suiten ist er in der Lage, eine Verbindung zu verschiedensten Systemen herzustellen und deren Daten im OPC UA Format bereitzustellen. Darüber hinaus überzeugt der OPC Server von Kepware mit seinem umfangreichen Sicherheitskonzept sowie erweiterten Plug-ins, die unter anderem eine IIoT-Konnektivität unterstützen.
Sie können den KEPServerEX kostenlos und unverbindlich testen. Fordern Sie noch heute Ihre persönliche Demo an.